FPSO Terra Nova Internal Disconnectable Turret
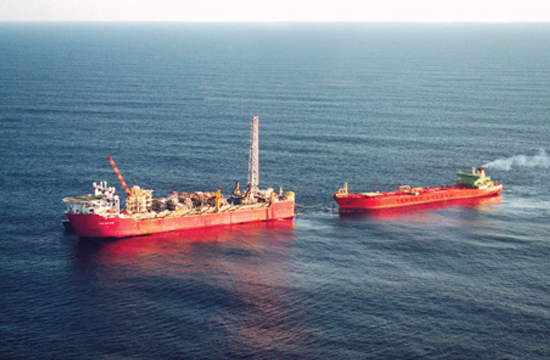
Scope of Work
SOFEC designed and engineered an internal disconnectable turret system in the Terra Nova FPSO. The SOFEC turret permits the vessel to disconnect and reconnect to the mooring to avoid icebergs and severe sea ice conditions. Time for planned riser and buoy disconnect is less than four hours and is fully reversible up to final disconnecting command. Time for emergency disconnect is approximately fifteen minutes. The swivel stack consists of low and high pressure fluid swivels, low and high pressure utility swivels, power and optical swivels. The turret uses a nine leg group catenary chain with a heavy excursion limiter mooring system.
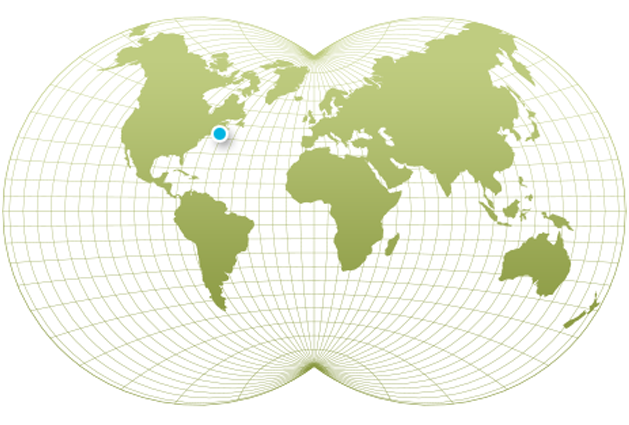
General Description
Client Name: | Petro-Canada |
Contract Award: | January 1997 |
Installation Date: | August 2001 |
First Oil: | January 2002 |
Hull Displacement: | 193,000mt (full load condition) |
Storage Capacity: | 960,000 bbls |
Water Depth: | 95m (312ft) |
Fabrication: | Turret - Abu Dhabi Vessel - Korea Topsides - Newfoundland and Scotland |
Design Environmental Criteria
(100-year storm)
Significant Wave Height: | 16m (52.5ft) |
Wind Velocity: | 39.6m/s (77 knots) |
Current: | 0.9m/s (1.7 knots ) |
Mooring System
Turrets
9-leg (3×3) grouped catenary:
5.375-in. Grade 4 studless chain
Excursion limiter (1471kg/m)
(5) 5MW thrusters with combined total thrust
available of approximately 450mt
Spider Buoy—The spider is a 12-compartment buoy, 17m in diameter and approximately 8m high. The buoy has a displacement of 1,700mt and a mass of 1,250mt, providing a net buoyancy of 450mt.
Lower Turret Structure—The lower turret structure is an internal turret, which provides the load transfer between the turret system and the vessel, and houses the equipment turret system and the
vessel, and houses the equipment required for disconnection and reconnection of the FPSO and the spider buoy including the riser QC/DC connection.
Upper and Lower Bearing Assemblies—The vessel loads are reacted into the turret through an upper bearing assembly and a lower bearing assembly. The upper bearing assembly consists of a three-row roller bearing mounted on a support structure. The lower bearing assembly consists of eighteen individual self-lubricating bearing segments arranged evenly around the bottom of the turret.
Connector Tensioner Assembly—The connector tensioner is comprised of a large FMC Torus connector and a specially designed large bore hydraulic cylinder (tensioner). After pull-in of the spider buoy, the
connector is mated to the hub mounted on the spider buoy and the tensioner is activated hydraulically, pulling the spider buoy tight against the mating profile of the lower turret.
Upper Turret Structure—The upper turret structure supports all turret components located above the main deck of the vessel. The structure consists of three decks built around the swivel stack and along the centerline of the vessel. The first two decks are dedicated to turret piping, manifolding, and pig launching and receiving stations. The upper deck is a control deck, which houses the local equipment room and hydraulic power units.
Fluid Swivel Assembly
Production: | 2 x 16-in. (740 psi design) |
Production / Test: | 1 x 12-in. and 1 x 10-in. toroid (1,480 psi design) |
Fire Water: | 1 x 10-in. toroid (285 psi design) |
Flare Gas: | 1 x 12-in. toroid (285 psi design) |
Gas Injection: | 1 x 6-in. toroid (5,932 psi design) |
Gas Lift: | 1 x 6-in. toroid (4,190 psi design) |
Water Injection: | 1 x 10-in. toroid (5,000 psi design) |
High Pressure Utility Swivel: | 8 x 0.75-in. path for methanol & inhibitors (5,500 psi design) |
Low Pressure Utility Swivel: | 8 x 1-3-in. path for air, hydraulic, nitrogen, steam (285 psi design) |
Electrical Power Slip Ring: | 12 rings, 150-600 amps, 220-600 volt ac |
Control Signal Slip Ring: | 72 rings |
Optical Slip Ring Swivel: | 12 paths |
Riser System
8 x 10-in. Flexible riser
3 x 9-in. Flexible riser
1 x 7-in. Flexible riser
2 x 5-in. Flexible riser
5 Umbilicals (power, signal, high and low pressure hydraulic,
injection & annulus bleed
Comments
The Terra Nova field is located on the Grand Banks in 95m of water, 350km East-Southeast of St. John’s, Newfoundland. The oil field will be developed using a floating production storage and offloading facility and subsea wells, with crude oil transported to market by shuttle tankers.
The FPSO is a purpose built, ice strengthened FPSO with forward accommodations and a disconnectable internal turret mooring system located just aft of the accommodations.
The FPSO, which is part of a full field development supplied to Petro- Canada by the Terra Nova Alliance and includes reservoir, drilling/ completion, subsea wells, manifolds, flowlines, and flexible risers.
Subsea facilities for the first phase of the development will consist of 24 subsea wells manifolded on templates flowing through flowlines to flexible risers that terminate on the floating production facility.
The Terra Nova Alliance, a consortium of companies, led by Petro- Canada conducted the project. The Alliance consisted of: FMC Offshore Canada Company, Shawmont Brown & Root, Halliburton Energy Services, PCL Industrial Constructors, Coflexip Stena Offshore, and Doris ConPro.
The SOFEC disconnectable internal turret mooring system is classed with
Lloyd’s.